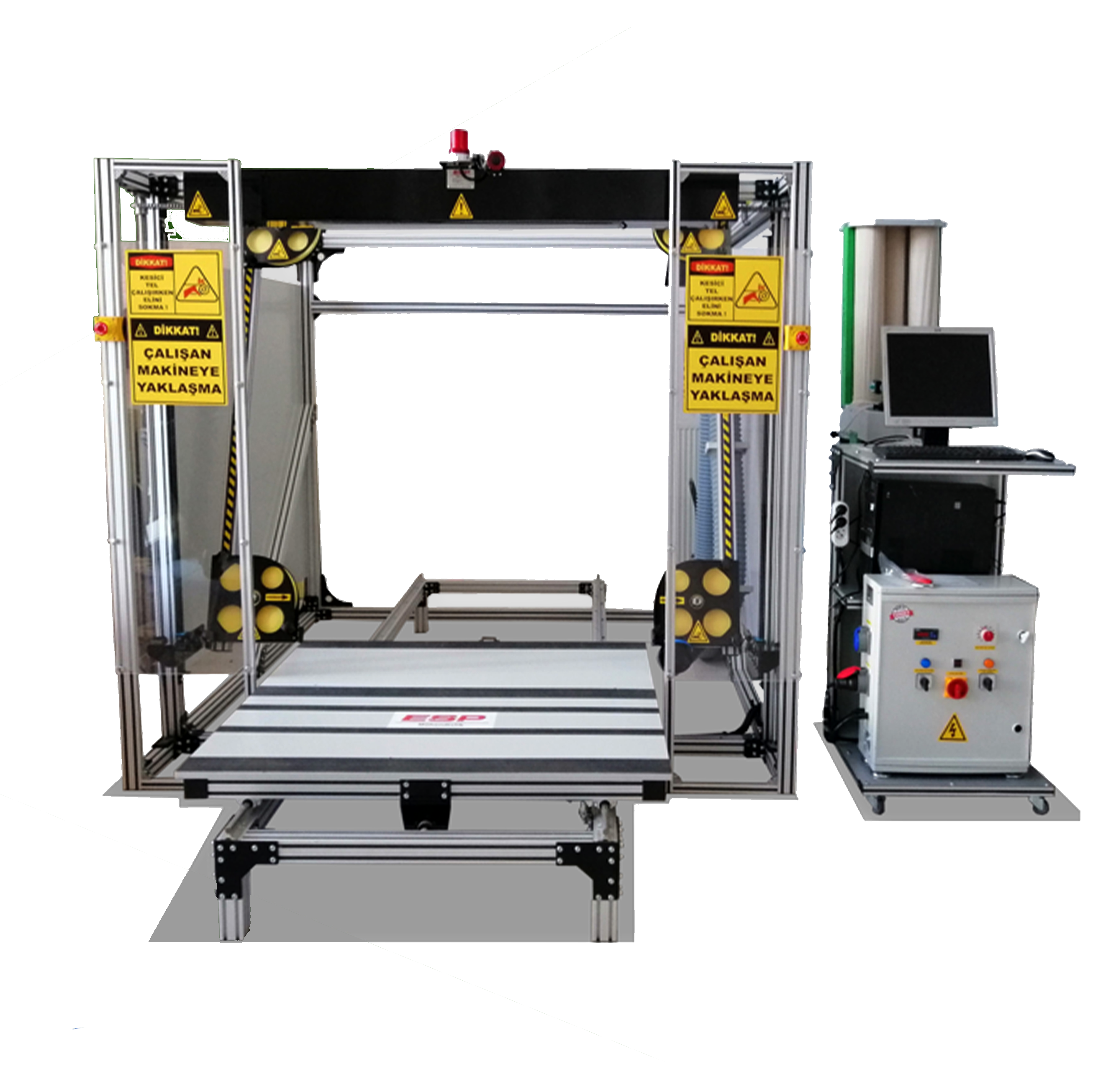
What is Fast Wire Cutting?
Thanks to the computer aided CNC cutting machines, Fast Wire Cutting makes it possible to make precise shaping on the material being cut and to obtain smoother surfaces by moving the cutting wire very quickly. Fast Wire technology, combined with the processing power of CNC machines, extracts the desired product shape from the material blocks in the most professional way. The wires used in this process are called fast cutting wire, and the machines are called Fast Wire CNC Cutting Machines.
Which Products Can Be Fast Wire Cut?
Rock wool , Polyurethane (PU) , Glass wool , Sponge , ytong ve Turkish Marble Many different materials can be cut with Fast Wire Cutting technology according to the usage area, especially the materials. These materials, including the cylindrical shapes required for processes such as rock wool pipe insulation, can be cut with the most precise settings.
What is the Difference Between Fast Wire Cut and Hot Wire Cut?
Fast wire cutting works on the principle that the cutting wire moves very quickly and turns into a very precise moving saw. Hot wire cutting, on the other hand, is based on the principle of shaping and cutting the surface precisely by melting the cutting wire by heating it to high temperatures.
Fast Cut Wire Material and Usage
As ESP Engineering, we produce cutting wires with different properties used in fast wire cutting. Used in cutting polyurethane PUR – Polyurethane Cutting Wire, for Stone Wool Cutting WOOL – Stone Wool Cutting Wire and sponge cutting SPONGE – Sponge Cutting Wire each has a customized surface and features according to the materials.
Since the Cutting Wires come into direct contact with the surface during cutting, abrasions may occur due to the friction force based on time. For this reason, in terms of occupational safety, you should not neglect to renew the wires of your CNC cutting machines within their lifetime.
Fast Wire Technology Technical Details
You can browse the machine specifications pages to get more detailed information about fast wire cutting and to discover Fast Wire Cutting Machines.
To write a comment you must log in.